Blisters are among the most familiar packages found in retail settings. The versatile packaging solution encompasses a number of styles, including clamshells, trapped blisters and boxed blisters. With applications across the entire commercial packaging spectrum, blisters house diverse products, from high-end electronics to children’s toys.
The correct blister package for a given job depends upon the item to be enclosed and its unique marketing requirements, as well as any other brand imperatives. With these considerations in mind, producers from food, pharmaceutical, cosmetics, and other industries consult with packaging providers to meet their particular needs. And while the shared goal is bringing goods to market, there is more than one way to get the job done with blister packaging. Today’s trends include innovative advances like boxed blisters that use less material, and pharmaceutical blisters, which continue to grow more popular.
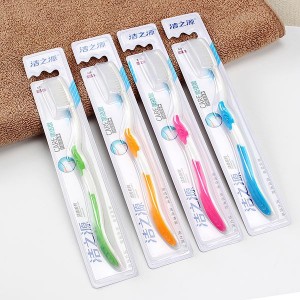
Weighing The Benefits Of Blister Packaging
Each industry using blister packages selects them for unique reasons. For some, merchandising is an important consideration, as well as protecting goods. In other cases, blisters furnish the best path to regulatory compliance. Still other producers rely on tamper proof versions for enhanced security on retail sales floors. It is this versatility, which makes blisters ideal for so many different products.
Custom Forming – Blisters are formed using heat, or in some cases cold-pressed. As a result, they can be made in almost any conceivable shape, which often follows the contours of packaged items. Molding blister packages in precise shapes provides cushioning for individual items, which are securely cradled during shipment. And custom shapes also reinforce brand identity, as repeat customers begin to associate unique package shapes with their preferred products.
Visibility – In many cases, the closest thing to actually handling a product is a shopper’s ability to feel its outline through a molded blister pack. And since most packages are clear, the items inside are highly visibility to curious consumers. Without damaging them or creating shop worn goods, consumers get a feel for the heft of products, easily inspecting product features at the same time.
Merchandising Value – Blister packaging can be outfitted with hang holes and other merchandising features. And the glossy appearance of thermoformed plastic elevates perceived product value, making blisters appropriate for a wide range of price points.
Product Protection and Integrity – Keeping goods secure at each stage of the consumer supply chain is an essential feature of product packaging. And since rigid plastic packages offer built-in protection, blisters furnish adaptable solutions for a variety of goods. Not only are blister packs safe from tampering, but they can be outfitted with special materials to inhibit exposure to moisture, air and potential contaminants.
Boxed Blister Packaging
Blister packages are typically made of PVC, incorporating various supporting materials to complete each package. A blister card, for example, bonds the molded plastic feature to a sturdy backer designed for hanging or merchandising in a counter tray. And traditional “trapped” blister packages employ two cards or a folded card to entirely encapsulate the blister package seams.
Boxed blisters, on the other hand, perform similar functions, but don’t “trap” the blister package portion in the same way. Instead, boxed blisters are assembled by sliding the molded plastic forms into paperboard sleeves. The blisters are then held in place by folded tabs on the sleeves.
In addition to standard benefits of blister packaging, boxed blisters also present distinct advantages. For starters, constructing blister packages in this manner reduces the amount of materials used. The blister itself uses less plastic, and the sleeve requires less paper than traditional cards and folded enclosures.
Steady Growth In Pharmaceutical Packaging
Foil Blister Packaging – CardedBlister packaging does not have the same history in the United States that it does in European markets. In Europe, a large share of pills, tablets, and capsules are dispensed from single-dose blister packs, while the United States has traditionally favored bottles and jars. Tides are turning, however, as pharmaceutical and supplement producers recognize the convenience and effe
ctiveness of blisters. In addition to tamper-resistance and product protection, single-dose unit blisters increase patient compliance, by making doses easier to track.
Constructed of formed plastic sheets and foil or paper backs, blisters serve over the counter customers as well as prescription clientele. Within the global pharmaceutical packaging industry, blister packs are estimated to account for about 17% of the market. This already represents more than eight billion USD in annual revenue, but pharmaceutical blister packaging is expected to continue making gains over the next five years. New FDA regulations mandating single-dose packaging in hospitals can only add to the blister boom.
Between 2015 and 2019 the pharmaceutical blister pack industry is expected to grow by 6%, reflecting increased demand and blister packaging innovation. Boxed blisters and other responsible packaging practices will also gain ground, as consumers align themselves with brands that share their values. Economy, product integrity and versatile merchandising capabilities will continue to drive producers toward blister packaging solutions, but the ultimate test lies with consumers, who appear to be embracing the benefits of user-friendly blisters.
FROM:Assemblies